PROCESS FLOW OF PRODUCTION
At the initial stage, different types of yarn have been brought from local and international yarn manufacturer, and the accessories are collected from backyard-linkage industries of local and foreign origin. At the next step, raw package of yarns are rolled up for giving those suitable revolving shape and sent those to Yarn Distribution (YD) section, where every spin of yarns has been properly weighted, and specific amount of spindled yarn has been allocated to the Knitting section.
Every part of sweater is knitted in the knitting section and passed them off First Inspection to get those checked whether each part is properly knitted or not, and to get confirmed if any yarn is wasted. After First Inspection, each part of the sweaters is linked up in the linking section and thoroughly checked in the Second Inspection and then to light checking with a view to ensuring if any hole is present in the sweater.
Accurate measurement is tested in the Third Inspection; if it is found up to the standard, the sweaters are passed through the labeling section, where neck, care and size label are attached. Steam ironing is performed after labeling and sent them in the quality control section, where each part of sweater is checked carefully, thus if the sweaters are found not up to the standard, they are sent back to the Third Inspection section for mending the loopholes. Whole process of knitting is being examined at final inspection section, and passed them for packing or folding. After packaging, whole lots are transferred into the warehouse and keep them standby for shipping.
For the ease of understanding the sweater manufacturing process, a processing lay-out is presented here.
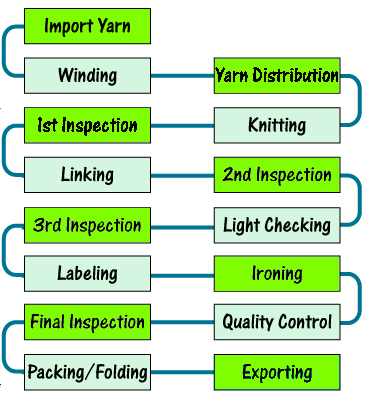